Taking targeted action, pharmaceutical manufacturers can advance their operations in a way that is rapid, cost-effective and does not need process re-validation. The solution lies in automating off-line testing in analytical laboratories. By doing this, companies can streamline quality control while enhancing data integrity and regulatory compliance, ultimately cutting downtime and cycle times.
Martin Gadsby, VP at Optimal Industrial Technologies, looks at how to automate analytical laboratories to improve pharmaceutical operations.
The pharmaceutical industry is typically seen as resistant to change. This is understandable, as companies need to follow strict regulations to ensure product quality, consistency and safety, any modification of manufacturing processes requires costly and time-consuming re-validations.
At the same time, it is essential for pharmaceutical producers to drive up their competitiveness in an increasingly fierce and demanding marketplace as well as be ready to address new requirements from regulatory bodies. In particular, with the advances in digital technologies and supervisory agencies raising the bar on data-driven operations, forward-looking businesses are already beginning to implement smart, Industry 4.0 solutions.
In cases where upgrading a manufacturing line is not feasible due to re-validation requirements, pharmaceutical manufacturers can still begin their digital transformation journeys by focusing on their analytical laboratories. In fact, the implementation of innovative, automated technologies in these environments do not directly influence manufacturing processes.
As a result, these projects can be carried out with minimal investment while delivering considerable gains. Moreover, they can help users develop their automation and digital skills while providing the technical and financial tools to support future process modifications and successful re-validations.
A closer look at the benefits of automated laboratories
Batch processing in the pharmaceutical industry often leads to considerable downtime associated with quality testing activities. This activity can cover from 50% up to 80% of cycle times required for a small manufacturer to produce oral solid dosage (OSD) forms. In addition, the associated labour costs can account for more than two thirds of all operational expenses, which equates to approximately 10% of revenue.[1] Therefore, just by streamlining these tasks, businesses can intensify their competitiveness and reach new heights.
Innovative technologies can improve batch processes by means of, for example, automated testing of multiple samples and specimens. This can considerably reduce quality control time and cycle time, while freeing up lab technicians from the repetitive tasks associated with quality control. As a result, it is possible to increase the time they have available for value-added activities.
In addition, automated sampling based on robots, automated guided vehicles (AGVs) or other types of self-driven machines can support the collection and delivery of solid samples from production lines to off-line testing facilities. Liquid sampling can also be achieved by using specialised systems that transport the sample to the analytical laboratory.
Advancing data integrity now
While leveraging automated machines to speed up testing while maintaining high accuracy and precision is extremely advantageous, the cost of such projects may still be prohibitive for some companies. The most suitable solution for lower investment digital transformation projects is the use of automated laboratory solutions that input and store result data as well as reliable, fully computerised data management systems that benefit audits.
This can also support the future implementation of complete Process Analytical Technology (PAT) frameworks while facilitating any associated process re-validation. Moreover, it can simplify the adoption of additional digital technologies, such as Cloud and Edge computing.
To create such a setup, companies can leverage the digital transformation enabling software, synTQ. This supports total quality management for the pharmaceutical sector by providing a data management tool that is compliant with current regulations on electronic signatures and records (ERES), such as the U.S. Food and Drug Administration (FDA)’s 21 CFR part 11.
The platform is ideally suited to advance data transparency and integrity practices for quality auditing and regulatory compliance. As a result, businesses can ensure that their datasets are attributable, accurate, legible and complete, which ensures adherence to ALCOA+ principles.
In addition, synTQ offers Cloud data pump capabilities, whereby all data collected from different analytical instruments can be stored and analysed in a centralised platform to produce a holistic data-driven insight, in line with Industry 4.0 practices. In essence, the laboratories of the future are here to boost pharmaceutical operations.
[1]Cogdill, R.P., Knight, T.P., Anderson, C.A. et al. The Financial Returns on Investments in Process Analytical Technology and Lean Manufacturing: Benchmarks and Case Study. J Pharm Innov 2, 38–50 (2007).
Image 1: Automated laboratories can streamline off-line testing without requiring process re-validation. (Source: iStock: 1397544977)
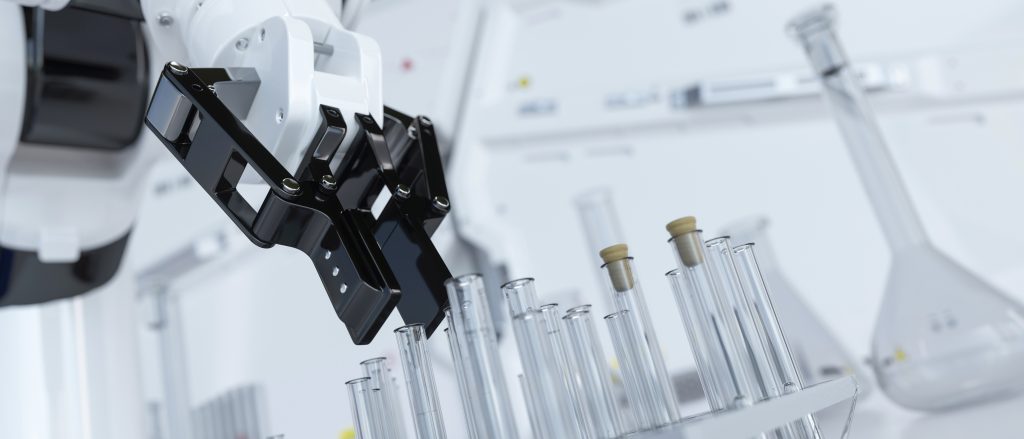
Image 2: An automated laboratory system that leverages a digital transformation enabling software, such as synTQ, can optimise product quality, regulatory compliance and manufacturing efficiency.
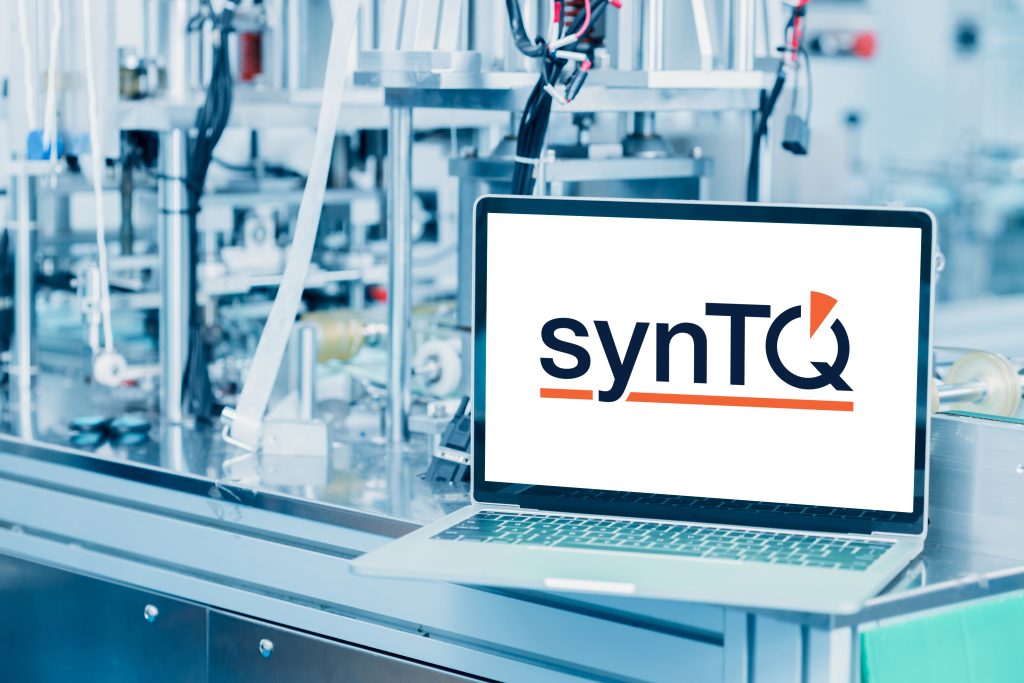