What is PAT?
Process Analytical Technology (PAT) is a powerful quality assurance tool that can revolutionise the productivity of automated process manufacturing facilities. Originally driven by the pharmaceutical manufacturing industry, the integrated approach is being adopted in fast-growing numbers by many other process industries, including food & beverage, FMCG, chemical and oil & gas. As process industries come under increasing pressure to deliver new products quickly, with improved quality and at reduced costs, PAT can provide substantial benefits in each of these areas.
PAT is a method to measure in real time the quality of intermediates and end product, and to control the process based on quality data as opposed to fixed, empirically derived recipe data. PAT leverages scientific, data-oriented approaches and methods to set up highly productive and efficient manufacturing processes.
The use of PAT provides the route for companies to establish a Quality by Design (QbD) approach to their production, which enables high quality products to be manufactured and verified in real time, rather than testing for quality after a process is completed.
Quality by Testing (QbT) is the traditional approach, but it is inherently wrong. With QbT, you are not steering the process in a quality-centric way, instead, you are testing too late in the process after value has been added to what may be a reject product. The QbT approach simply tests quality into the product, which is not optimal for productivity or quality, but until recently it has been the only option.
When properly applied, PAT is a key technology that has been proven to provide significant gains in terms of time and cost for the research, development, and manufacturing of products, whilst also delivering increases in quality and consistency.
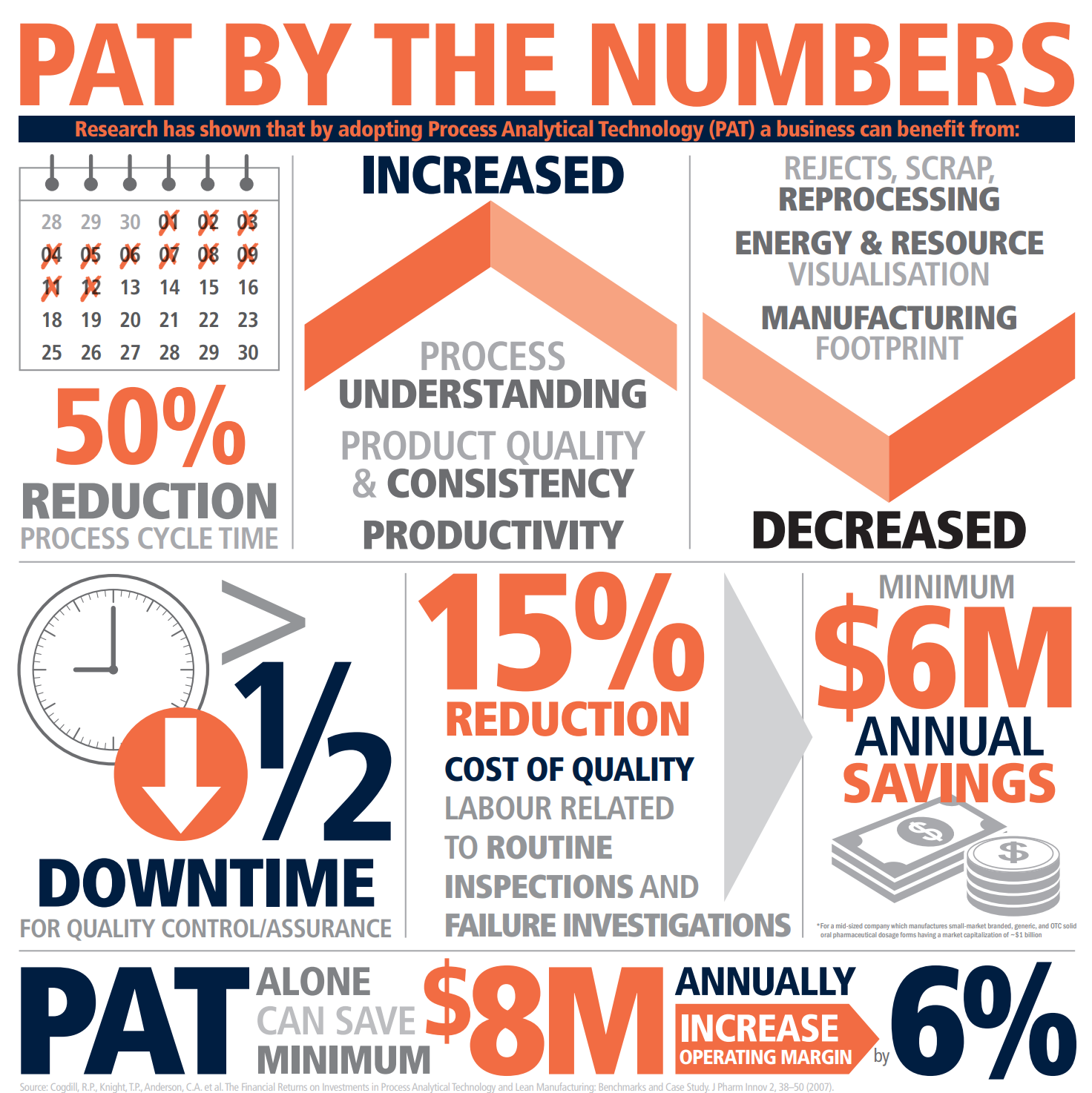
Source: Gadsby, M. (2021) PHARMA PRODUCTION COULD DOUBLE RIGHT NOW – USING ITS EXISTING MANUFACTURING FOOTPRINT… BioPharma Asia, 10(2).”
The improvements for manufacturers can be substantial. For example, the implementation of PAT for a biotechnology process has been reported to result in a threefold increase in productivity. In this example, the process was carried out using the existing batch manufacturing infrastructure. Other manufacturers are working towards even greater gains by moving to continuous manufacturing.
There are several examples of companies manufacturing in a continuous way, rather than by batch. The continuous approach is not possible without PAT, real-time quality assurance and, specifically, synTQ. By taking this approach, production times have been slashed from nominally 30 days to nominally 90 minutes – a 500-fold decrease in manufacturing time. This is a paradigm shift that enables just-in-time manufacturing.
Whether you are continuing to use batch manufacturing or transitioning from batch to continuous processing, by using PAT and synTQ with fully automated, multi-instrument, holistic quality assurance, you are able to realise Real-Time Release Testing (RTRT), where final product testing is no longer required.
“PAT is the key to enabling process industries to make the step change from inefficient, empirically-based production to automated, quality-centric manufacture. PAT facilitates the transition from batch to fully integrated, regulatory-compliant, continuous production.”
Martin Gadsby, CEO at Optimal