The concept of Process Analytical Technology (PAT) may not be familiar to manufacturers and processors outside the (bio)pharmaceutical industry, but they may already be leveraging aspects of it. By knowing what PAT frameworks can offer, businesses can take key steps to implement these value-adding elements into their practices. This can not only enhance their quality-to-cost ratios and profitability, but also effectively futureproof their operations.
Chris Vickers, Global Sales Manager at Optimal Industrial Technologies, looks at what PAT is and what it can deliver to manufacturers across various sectors.
The origins of PAT can be traced back to the early 2000s. This is when the U.S. Food and Drug Administration (FDA) introduced an initiative aimed at promoting a system of analysis and control strategies to monitor production processes in real time. The ultimate goal of this programme was to encourage pharmaceutical manufacturers to modernise their processes and adopt more science-based approaches to ensure product quality, and ultimately, patient safety.
Real-time monitoring of product properties, data analytics, process control, Quality by Design (QbD) and regulatory compliance represent the key pillars of PAT frameworks. While they fall into the domain of PAT in the (bio)pharmaceutical industry, these elements are also used in other industries by many companies leveraging process and factory automation. These include chemical facilities, as many of them use on-line monitoring for control purposes.
More than process control
The individual PAT components mentioned above are rapidly growing in popularity, especially as more industry players embark on digital transformation projects. However, while the adoption of even a single element can deliver benefits, the creation of a complete PAT setup can add considerable value to the operations of any manufacturer – whether they are serving the (bio)pharmaceutical or other markets.
The on-line monitoring systems typically used in the chemical sector, for instance, are often limited to univariate measurements and use basic and relatively linear predictive models. As a result, only partial product or process insights are gathered, rather than overviews that are both holistic and granular. However, companies that already have elements of automated process control, even if rudimentary, can use them as the backbone to create more comprehensive PAT frameworks.
For example, manufacturers can include the monitoring of multivariate data, such as infrared or Raman spectra, to generate process and product knowledge. This, in turn, can help build a clearer understanding of what determines quality in products and how to efficiently achieve it. By incorporating this additional information, it is possible to enhance quality and consistency as well as improve cycle times.
A clear example of how PAT can optimise productivity and profitability can be found in its adoption for the production of powders, especially solid mixing. Often, the automated processes involved use pre-set run times that do not account for the specific properties of the initial feedstock and can favour over-processing.
By moving to more responsive, automated frameworks, companies can minimise cycle times and energy usage without affecting product quality or consistency. These PAT-driven solutions can even improve quality, as overmixing also has the potential to alter key physicochemical attributes, leading to issues such as constituent separation and heterogeneity. Installing feedback/feedforward control based on real-time monitoring can prevent this.
In addition, by having a thorough characterisation of raw materials and being able to adjust processes in line with the specific physicochemical properties, companies can also effectively handle more variable feedstock. This, in turn, can enable manufacturers and processors to use resources more economically or diversify their supply chains, ultimately driving resilience and profitability.
How to embrace PAT
Embarking on a PAT implementation journey can be remarkably easy for companies that already use process and factory automation solutions, as most if not all manufacturing companies already have the right mindset to support a PAT-friendly culture. To succeed in a value-adding, stepwise adoption of key technologies, it is important to define what processes would benefit the most from enhanced analytics and control capabilities. These should be prioritised and, once completed, other areas of the business can be considered. Subsequently, to maximise the impact of PAT, it is recommended to move from “islands”, where the technology is used in an isolated way, to a holistic approach that encompasses production as a whole.
To drive the creation of highly effective PAT setups, partnering with a specialist that can provide comprehensive support is key. Optimal is a leader in the sector, with decades of experience, offering a single point of contact to realise any PAT implementation.
The company can deliver vendor-neutral solutions that leverage the most suitable equipment to support each individual project, including the market-leading PAT knowledge management platform, synTQ. In addition, Optimal experts and consultants can provide extensive after-sales support, streamlining installation and startup as well as training users to ensure smooth operations. By partnering with Optimal, manufacturers and processors can succeed in their PAT journey and enhance their competitiveness.
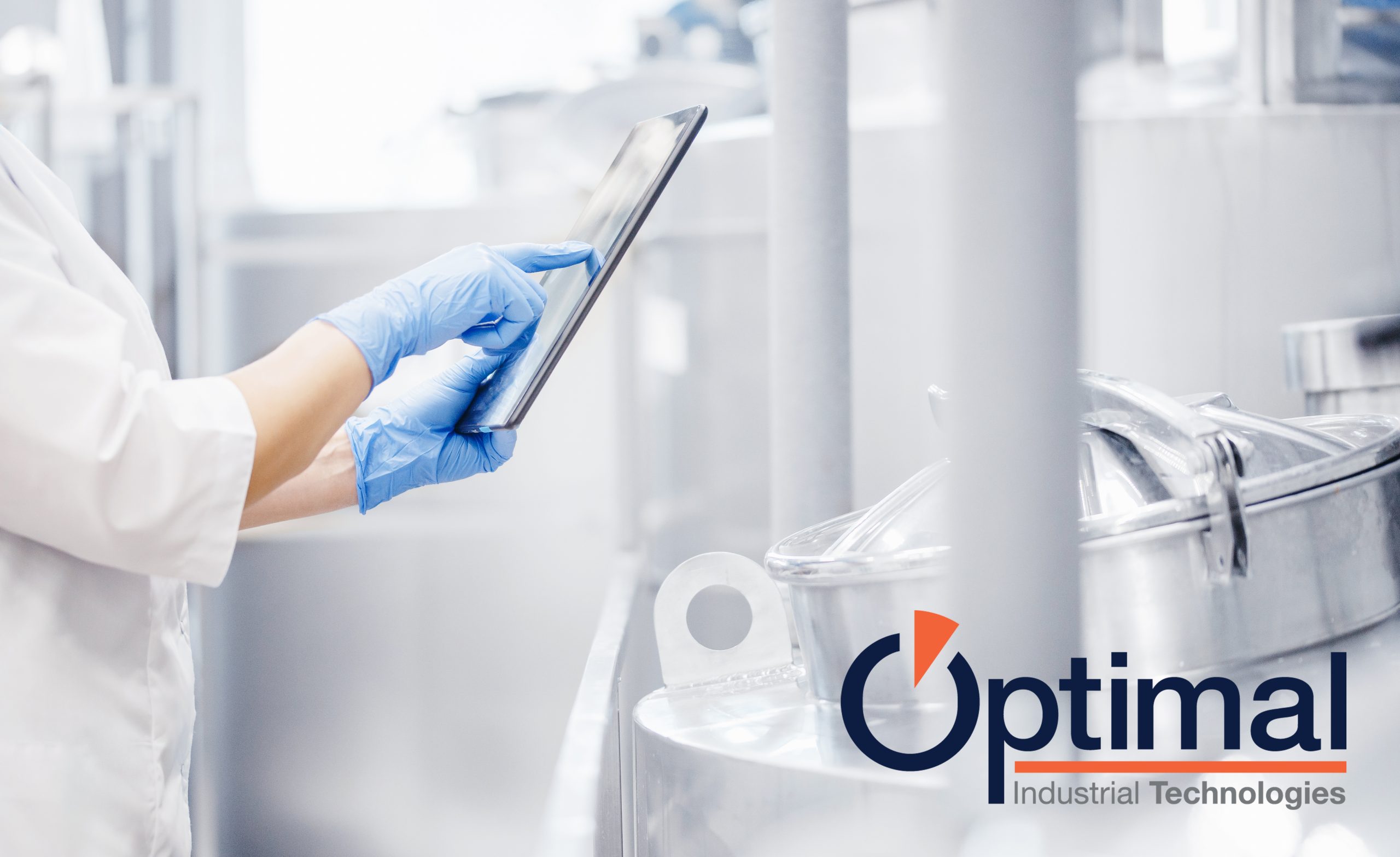
Image 1: Optimal is a leader in the Process Analytical Technology sector, with decades of experience, offering a single point of contact to realise any PAT implementation.