How does PAT work?
The PAT framework is used to analyse raw and in-process materials together with final product in real time by using in-line or on-line analyser instrumentation. Complex, multivariate instrument data is interpreted, from which the critical process parameters are adjusted to optimise the outcome of the process. The analytical results make it possible to predict the quality of the end material, and to understand how altering critical process parameters (CPPs) will affect the process and end product.
The prediction of critical quality attributes (CQAs) is made in real time by analysing the often spectral instrumentation data with mathematical and statistical procedures known as multivariate analysis (MVA – and also known as chemometrics). In turn, by executing experiments where real-time quality predictions are made, it is possible for the relationships between the CPPs and CQAs to be established, so that true process understanding is developed. Armed with this knowledge, it is possible to ‘close the loop’ and control the process using real-time quality predictions.
The prediction of critical quality attributes (CQAs) is made in real time by analysing the often spectral instrumentation data with mathematical and statistical procedures known as multivariate analysis (MVA – and also known as chemometrics). In turn, by executing experiments where real-time quality predictions are made, it is possible for the relationships between the CPPs and CQAs to be established, so that true process understanding is developed. Armed with this knowledge, it is possible to ‘close the loop’ and control the process using real-time quality predictions.
The central software processing entity is known as a PAT knowledge manager. Optimal’s synTQ is the market-leading PAT knowledge manager. This software collects data from multiple instruments and sensors, then converts them into meaningful information and actionable insight. PAT knowledge managers also function as process orchestrators that analyse and store data, turning this into knowledge to optimise manufacturing processes. This not only offers plant operators a platform to control production processes based on quality predictions, but also provides a mechanism for continual improvements.
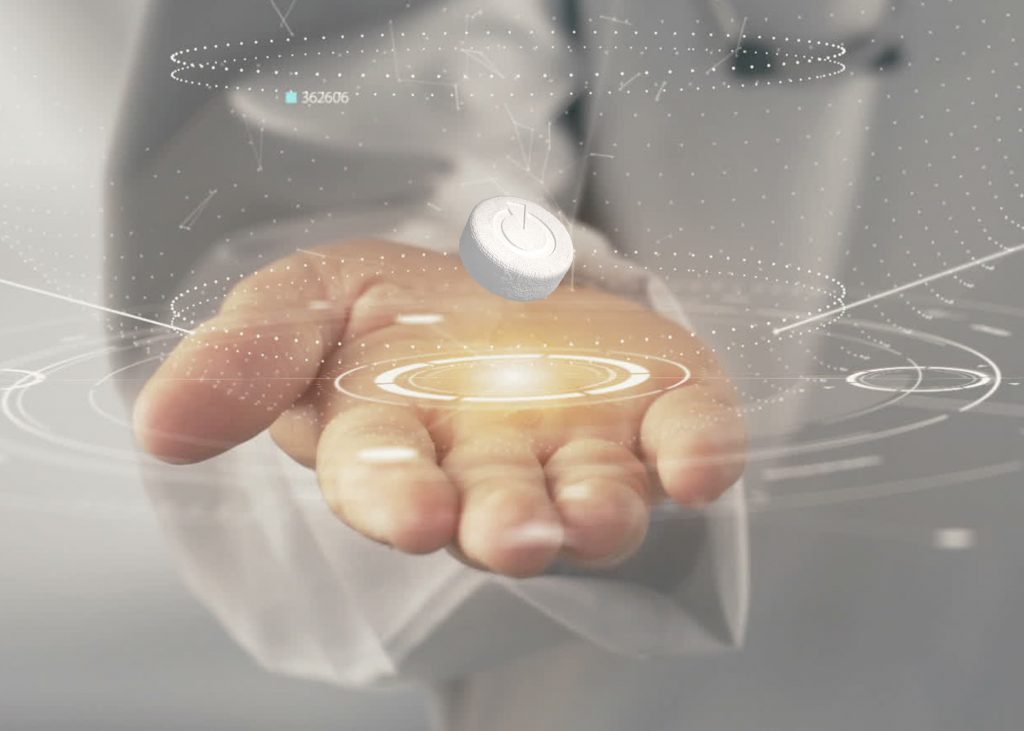
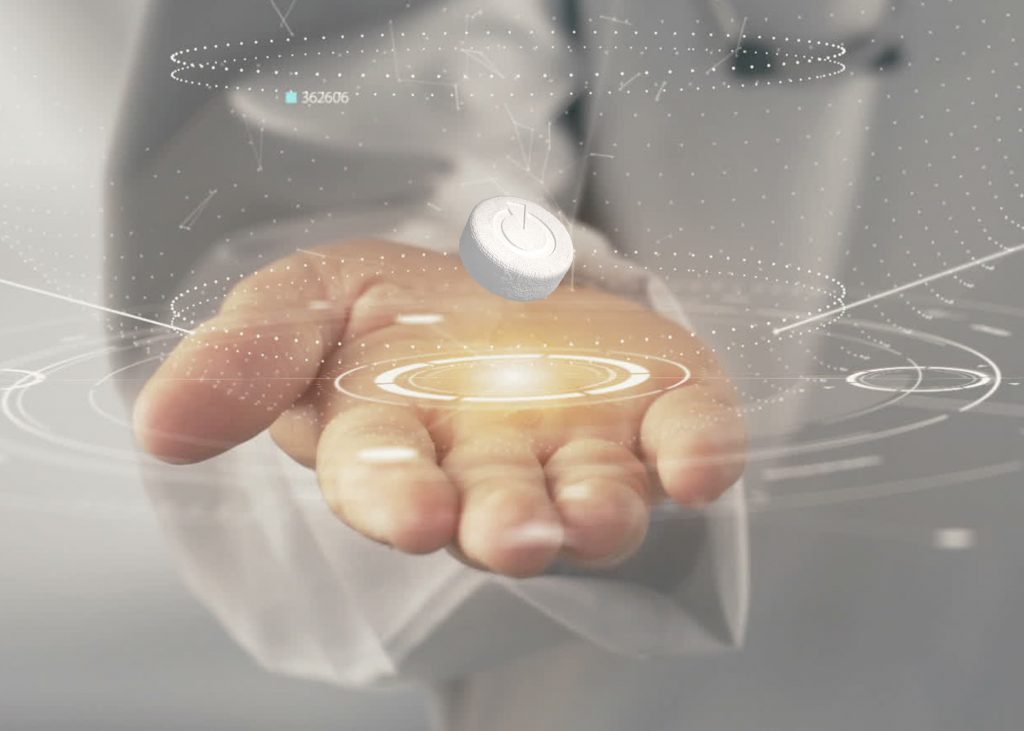
The prediction of critical quality attributes (CQAs) is made in real time by analysing the often spectral instrumentation data with mathematical and statistical procedures known as multivariate analysis (MVA – and also known as chemometrics). In turn, by executing experiments where real-time quality predictions are made, it is possible for the relationships between the CPPs and CQAs to be established, so that true process understanding is developed. Armed with this knowledge, it is possible to ‘close the loop’ and control the process using real-time quality predictions.
The central software processing entity is known as a PAT knowledge manager. Optimal’s synTQ is the market-leading PAT knowledge manager. This software collects data from multiple instruments and sensors, then converts them into meaningful information and actionable insight. PAT knowledge managers also function as process orchestrators that analyse and store data, turning this into knowledge to optimise manufacturing processes. This not only offers plant operators a platform to control production processes based on quality predictions, but also provides a mechanism for continual improvements.
Using the insights provided by the PAT knowledge manager, plant operators (or synTQ itself) can modify process conditions to support the delivery of end materials with high quality – the CQAs being dependent on your specific product. Moreover, the technology can handle the occurrence of variations in raw material characteristics. These fluctuations, detected at the beginning of the process, can be managed and compensated for by making knowledgeable and pre-emptive feed forward process changes. This would not only reduce the volume of poor-quality end products to a minimum, but also allow you to produce high quality end product with perhaps lower cost raw materials.