The pharmaceutical sector is here to help people live healthier lives. But without a healthy planet, this action is compromised. Therefore, pharmaceutical manufacturers should act now to reduce their emissions and contribute to ambitious net zero targets. By adopting data-driven technologies that characterize Industry 4.0, such as Process Analytical Technology (PAT), companies can reduce the environmental impact of their processes and products. They can also futureproof their facilities, improving their profitability and competitiveness in an increasingly challenging and demanding marketplace.
Martin Gadsby, VP at Optimal Industrial Technologies, looks at how PAT can reduce the environmental footprint of your operations.
Pharmaceutical production is one of the largest producers of greenhouse gasses (GHG) in the manufacturing industry, exceeding even the emissions of the global automotive sector. In fact, data suggests that the aggregate global emissions of the two in 2015 amounted to about 52 MMt-CO2e and 46.4 MMt-CO2e respectively [1]. One of the reasons for the extended environmental impact of pharmaceutical manufacturing lies in the chemicals used. These are often hazardous and require processing prior to disposal, further increasing the carbon footprint and the volume of waste generated.
There is a further differentiator between the pharmaceutical and automotive sectors that greatly contributes to increasing the emissions of the first. This is the level of digitalization, an aspect that has been the pillar of effective car manufacturing for years but is still lacking in pharmaceutical companies. The automotive industry has long been using highly interconnected robots and automation systems, predictive and workflow-managing algorithms, process and product visualization, as well as monitoring and control technologies.
These solutions play a key role in optimizing resource and energy utilization while reducing cycle times, waste, reworks and giveaway. The result is improved efficiency of production lines and product quality coupled with increased profitability. As policies and legislations worldwide are demanding that businesses reduce their carbon footprint, it is crucial for drug manufacturers to not delay the implementation of future-oriented digital transformation strategies that can make their operations and products greener.
A closer look at analyzers
Data-driven solutions, such as PAT, are among the most beneficial to pharmaceutical manufacturers. They can improve machines, processes and products by enhancing their visualization, monitoring, control and understanding. These changes improve decision making, in terms of responsiveness and accuracy. To create such a setup, companies should first consider what information is required and which datasets are necessary to deliver it.
With a broad range of sensors and analytical instruments available, it is important to identify the options that are best suited to meet the intended objectives, while also addressing budgetary or temporal restrictions as well as any additional requirement within a given process, facility or enterprise. For example, pharmaceutical companies should determine the type of information that is provided by the instrument. In addition, they should define the limit of detection, accuracy and response characteristics that should be offered by a given analyzer. Additional aspects include outlining the environmental conditions that should be withstood and those which are necessary for successful testing.
To generate a comprehensive overview of what is happening on the shop floor, it is also crucial to favor sensors and instruments that can be part of a broader network infrastructure to avoid the creation of ‘islands of automation’ that do not support data sharing. As vendor-specific PAT solutions are often limited in their ability to connect with pieces of equipment developed outside of the organization that created them, a company could decide to specify only products from a selected brand. This solution may not always be feasible when looking at the costs involved and vendor-specific analyzer portfolios. Alternatively, pharmaceutical manufacturers can implement vendor-agnostic software to collect, store, process and interpret the data from different sensors and instruments.
Merging it all together
This second solution is highly beneficial, as it empowers companies to install the analyzers that are best suited to address a given application. In addition, it provides a key tool to generate holistic process understanding, monitoring and control strategies. By implementing a PAT knowledge management platform, such as Optimal’s synTQ, it is possible to leverage a central hub for all data from sensors and analytical instruments. Such a management system can then combine the information via data fusion strategies.
By performing joint analysis of multiple inter-related datasets that provide complementary views of the same phenomenon, businesses can gain inferences that are more accurate than those that the analysis of a single dataset can yield. As a result, it is possible to create highly accurate predictive models on product quality. These can determine issues such as over-processing, which is inefficient in terms of resource utilization and run times.
Based on the insight offered by these models, the PAT knowledge manager can use automated process control solutions to directly signal setpoint changes to processing parameters in the automation controller such as a PLC or DCS. It can also inform users of any manual adjustments required to the operating conditions to avoid sub-standard outputs, wastage, reworks and giveaways.
A clear example of how this can be beneficial can be found in bioreactor applications, typical of biotechnology and life science facilities. To deliver optimum conditions for cell cultures, companies could set up in situ sensors for temperature, pH and oxygen as well as analyzers to measure glucose levels and the concentration of other metabolites. When these factors are linked through a PAT knowledge management software, it is possible to correlate and fuse the information from these multiple sources to have a clear view of what process condition changes are needed to maintain the optimum cell culture conditions in the most effective manner. When automated process control is in place, this actionable insight is transmitted to the relevant automation controllers to adjust the parameters accordingly.
Similarly, in processes such as blending and mixing, it is possible to avoid both under- and over-processing. These can lead, respectively, to poor quality and prolonged energy usage and cycle times – elements that increase rework, waste while reducing efficiency.
Supporting the entire value chain
The advantages of data-driven technologies are clear for drug fill/finish production lines, but they are also able to support the manufacturing of active pharmaceutical ingredient (API) and excipients as well as research laboratories and pilot plants. By applying the same principles of interconnected instrumentation and data fusion, R&D departments can enhance their process knowledge from the very early stages of drug development. Moreover, thanks to this actionable insight, they can replicate experiments in a digital space, saving time, energy and resources while cutting the waste generated.
Ultimately, the use of industrial automation and innovative technologies can have rippling effects across the entire value chain, making the entire sector greener and more efficient.
To enhance its sustainability – a requirement to meeting both regulatory and customer demands – the pharmaceutical industry needs to look at setting up automated strategies, such as PAT, to gather data and generate a unique business knowledge. By creating an interconnected network of analyzers and supporting advanced Big Data solutions, often using data fusion, pharmaceutical manufacturers can have a clear understanding of how their processes work, measure multiple quality attributes in real-time, and, if these are not optimal, know how they can be driven back to the desired state. By eliminating inefficiencies, more sustainable and profitable practices can become a reality, benefitting companies, patients and the environment.
References
[1] Belkhir, Lotfi; Elmeligi, Ahmed (2019). Carbon footprint of the global pharmaceutical industry and relative impact of its major players. Journal of Cleaner Production, 214, 185–194.
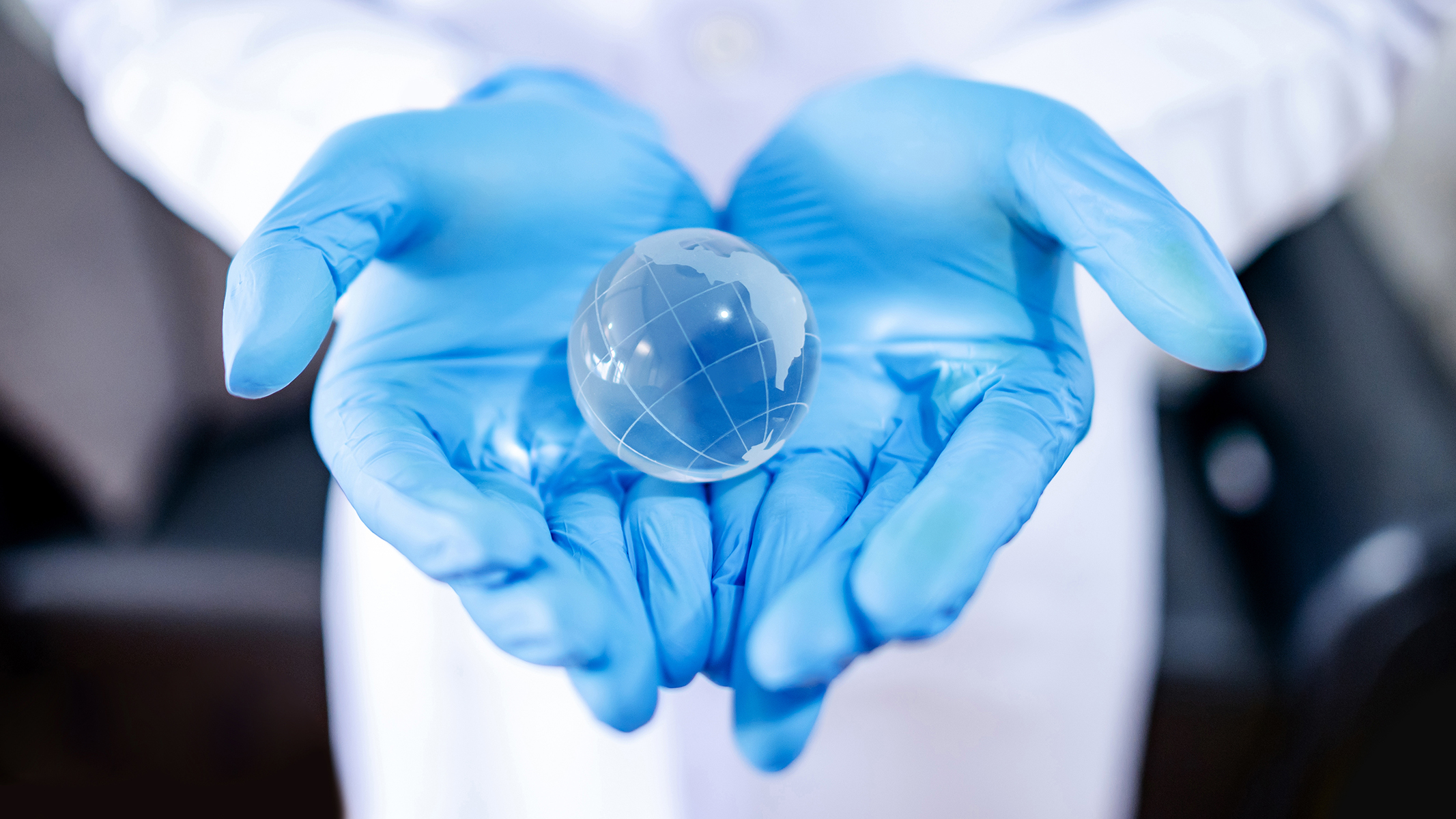