Optimal’s synTQ 5.5 enables holistic quality management
Optimal Industrial Technologies, a leader in Process Analytical Technology (PAT), has released version 5.5 of synTQ, its total quality management solution. The software offers advanced functions for data transparency and analytics, which will help manufacturers to improve flexibility and productivity by strengthening their process control, quality assurance and continuous improvement practices.
Optimal’s market-leading software for PAT-driven manufacturing, synTQ, provides a regulatory-compliant, scalable and modular central platform that supports companies’ total quality management activities. The software solution generates immediate actionable insight into R&D and manufacturing processes by creating a single interconnected network of instruments, analysers, management software and automation systems. As a result, businesses can enhance their efficiency, productivity and flexibility.
synTQ version 5.5 further enhances the system’s data analytics capabilities and functionalities to offer an even more in-depth process knowledge management platform. In particular, manufacturers can benefit from self-operated Automated Intelligent Control (AIC) functions for both batch and continuous quality-centric process control as well as Dynamic Flow Modelling (DFM) for real-time material tracking and tracing in continuous processes.
The latest version of synTQ also provides an update to the synTQ DX data pump functions, enabling the secure transfer of GMP-compliant and non-GMP PAT data to the Cloud for analysis and reporting. As a result, businesses can benefit from a scalable environment for Big Data analytics that can be used to implement innovative Industrial Internet of Things (IIoT) applications. Any regulatory-compliant GMP datasets transferred to the Cloud via synTQ DX can then also be used to support clinical trials across their different phases, regulatory review, and to scale up processes.
Finally, the latest release integrates Orchestration Digital Twin functionalities to run partial or complete PAT methods virtually, at any point during the process’s lifecycle. This allows businesses to create and test process data flows before running any real-world manufacturing activities. Once the virtual orchestrations have been created, tested and set, operators can systematically transfer the optimal operating conditions to the physical plant. This is particularly beneficial when implementing PAT processes in a manufacturing plant – especially so when the manufacturing operations are continuous.
Martin Gadsby, Director at Optimal Industrial Technologies, comments: “Thanks to its advanced, data-driven capabilities, synTQ 5.5 marks the transition from PAT knowledge management to total quality management. It offers a comprehensive solution to holistically improve manufacturing and processing operations. By leveraging advanced data transparency and analytics technologies, synTQ users will benefit from a futureproof platform that supports digital manufacturing strategies.”
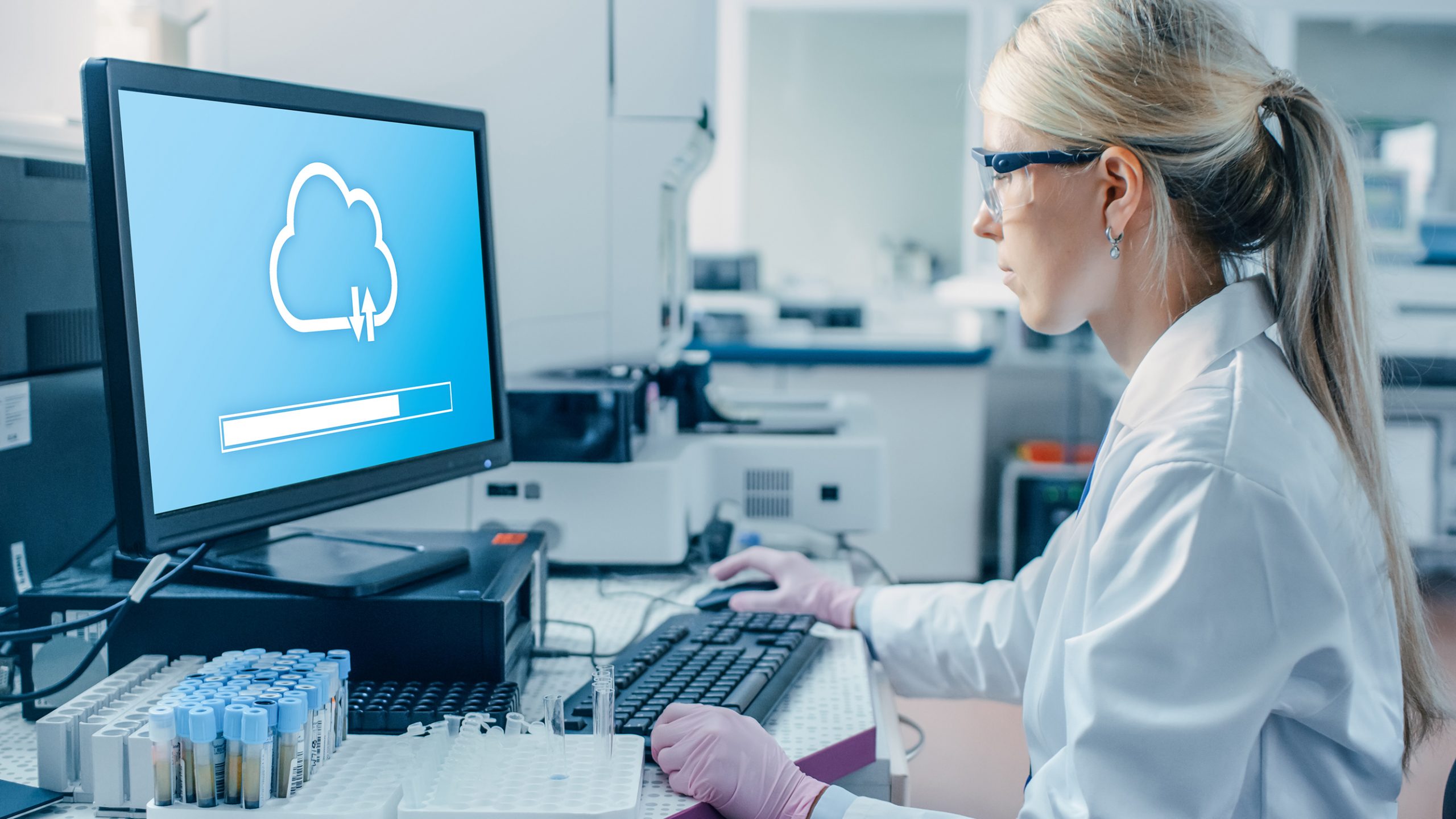
Photo Caption: By greatly extending the capabilities of PAT-driven operations, Optimal’s synTQ 5.5 can enhance competitiveness by improving efficiency, productivity and flexibility on the factory floor.
Image Source: iStock – 1140779649_gorodenkoff