Countless businesses have set their sights on achieving a true ‘digital transformation’ over the past decade, but many have struggled to turn these ambitions into reality. The exact reasons for this will vary from company to company, but one common thread is that they’re held back by poor planning and a lack of a solid framework. However, a key tool has emerged that can help manufacturers make these plans a reality: Process Analytical Technology (PAT).
As with so many business concepts, the exact definition of digital transformation is not the same for everyone. When it comes to the manufacturing sector, however, the generally agreed upon meaning is a business-wide transformation that leverages process and product data to boost business profitability, product quality, and manufacturing efficiency.
This approach puts data at the heart of any digital transformation effort. That means that if a project is to succeed, it must incorporate three key factors that link the digital world with the physical:
- Accurate, traceable, and verifiable data: Every piece of data must be correct, traceable back to its source, and confirmable for authenticity. Accurate data helps in making informed decisions, traceability allows for quick issue identification and resolution, and verifiable data ensures that the information used is trustworthy and can withstand scrutiny.
- Data with batch context: Even accurate data loses a lot of value if it’s presented out of context. Ideally, it should come bundled with all the associated metadata—information like time and date stamps, machine ID, batch number, etc. This ensures that any data-driven decisions made downstream are made with a full understanding of the wider picture.
- Total data integrity: The completeness, accuracy, and reliability of data must be maintained throughout its lifecycle. Data integrity ensures that information remains unaltered in unauthorized ways, accurate, and consistent from the moment it is recorded until it is archived. This is essential for regulatory compliance and making reliable, data-driven decisions.
How PAT can help
If you haven’t encountered it before, PAT is a framework for designing, analysing, and controlling manufacturing processes through real-time measurements of critical quality attributes (CQAs) and performance parameters.
By focusing on this data, PAT ensures that product quality is consistently monitored throughout a process, rather than relying on traditional manufacturing methods that use empirical testing carried out after its completion. By collecting and analysing data as it is generated, manufacturers can make swift adjustments to maintain optimal quality, reduce waste, and enhance efficiency.
This ability to systematically collect, categorise, and learn from product quality data helps to distinguish PAT from more conventional PLC/SCADA and DCS setups. While these systems are effective for basic control and monitoring tasks, they typically lack advanced data analysis, real-time quality management, and adaptive control capabilities. In contrast, PAT-based systems are capable of systematically collecting, categorizing, and learning from product quality data, enabling more sophisticated process control and optimisation.
It also makes it an ideal tool for businesses looking to launch digital transformation projects.
What PAT brings to the digital transformation table
Of course, plenty of manufacturers make use of PAT without enacting a full digital transformation. However, the framework’s ability to capture, analyse, contextualise and make available both real-time and historical data allows it to play a key role in enabling a smooth and effective digital transformation.
This role can be broken down into several key areas:
- Data capture and analysis: PAT enables the collection and analysis of data in real time, which is crucial for developing and refining the manufacturing models necessary for the digital transformation of a business. This continuous improvement loop helps improve processes over time.
- Support for traceability and compliance: PAT systems are designed to support traceability and compliance with regulatory standards, such as good manufacturing practices (GMP). This ensures that products meet stringent quality and safety standards.
- Transformation of data into actionable information: PAT technology helps transform raw data into actionable insights. This conversion is vital for making informed decisions and driving continuous improvement in manufacturing processes.
- Holistic data sharing and standardisation: PAT makes it easy to share data globally, ensuring compliance and standardisation from the laboratory to production. This capability is essential for multinational companies that need to maintain consistent quality standards across different locations.
- Support for continuous manufacturing: PAT supports continuous manufacturing by providing real-time data that helps maintain optimal production conditions. This leads to significant business and quality benefits, including reduced waste, rework and downtime; and improved product consistency.
The power of PAT
Ultimately, PAT frameworks empower manufacturers to stay competitive by maintaining high standards of quality and efficiency. They support continuous improvement, compliance with regulatory standards, and effective data management. When used as the backbone of digital transformation projects, PAT can help businesses achieve substantial productivity and optimisation gains.
Businesses ready to take their manufacturing processes to the next level, should consult with a respected PAT expert like Optimal Industrial Technologies. The company uses its extensive experience to guide customer through the implementation of PAT systems, helping to unlock new levels of operational excellence and fully realise the benefits of digital transformation.
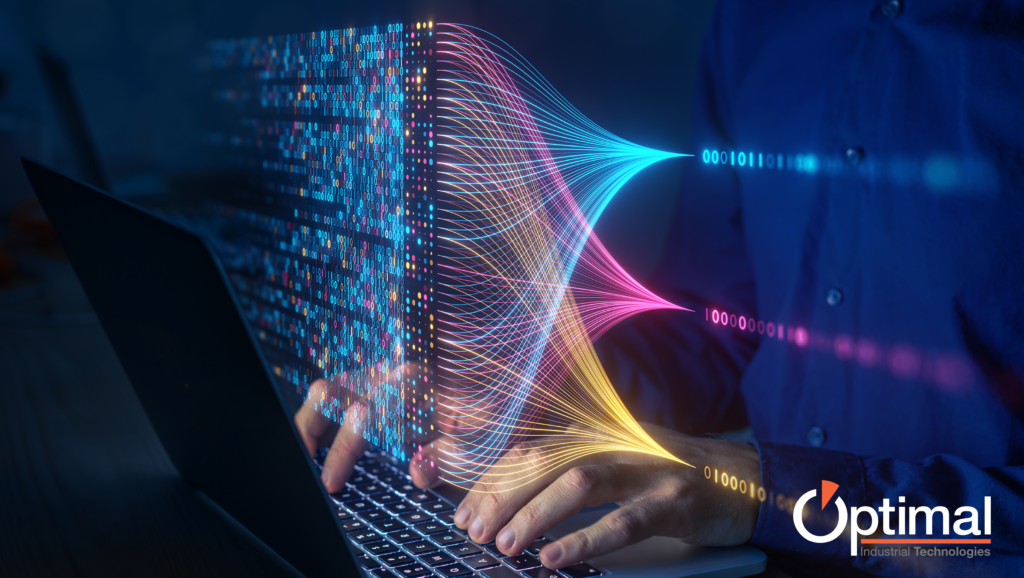
Image 1: PAT is a framework for designing, analysing, and controlling manufacturing processes through real-time measurements of critical quality attributes (CQAs) and performance parameters.